From entry-level machines to sophisticated system solutions, STUDER offers universal grinding, external grinding, internal grinding and non-circular grinding all from a single source. At this year’s GrindingHub, the Swiss quality manufacturer will be showcasing cutting-edge technologies from its current portfolio, including innovative developments in the entry-level segment, complex system machines and automation solutions.
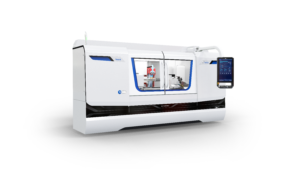
Highest precision in cylindrical grinding with the usual high STUDER quality: this also applies to the entry-level segment of the Swiss machine manufacturer. Models such as favorite, favoriteCNC and S100 combine the best of both worlds: economical standardization and top quality. At GrindingHub, the popular and versatile CNC universal external grinding machine will be on display for the first time with complete CORE equipment, including a high-resolution 24-inch touch control panel. You can also see for yourself the high grinding accuracy, excellent price/performance ratio, and wide range of applications of the CNC universal internal cylindrical grinder S100, which was released in the fall of 2022.
STUDER launches new automation system insertLoad
Customers can also rely on STUDER for complex system solutions for producing high-quality components individually, in small quantities or in serial production. Automation is becoming increasingly important in this sector, as this technology increases production efficiency and allows operators to work more easily, quickly, safely and with consistently high quality. That is why STUDER has developed automation solutions that are ideal for a wide range of applications. easyLoad (for S31, S33, S41, S22, S36), ecoLoad (for S22), smartLoad (for S11), uniLoad (for S31, S33, S36) and roboLoad (for internal cylindrical grinding S121, S131, S141 radius) for machines).
The latest automation solutions will also be on display at this year’s GrindingHub. S31 universal external grinding machine with insert load. This automation solution combines the benefits of standardization with great flexibility and can be operated via the CORE panel. As a versatile general-purpose external grinding machine, the S31’s modular system and high configurability make it suitable for small to large workpieces with different production requirements in individual, small-scale and large-scale series production. insertLoad can be used to automate STUDER S31, S33, and S36 machines. roboLoad will also demonstrate its capabilities in the S131 exhibit area. Radius machines for internal cylindrical grinding, such as the S131, are primarily used in the packaging industry where complex workpieces made of carbide or ceramics need to be machined. STUDER developed his roboLoad specifically for this field and can now also be operated via CORE.
WireDress® and SmartJet® grinding technology
STUDER is known for its industry-leading innovative grinding technology. The in-house developed WireDress® dressing process allows for less auxiliary time, higher precision and more economical operation when grinding with metal-bond CBN and diamond wheels. The process is based on the basic principle of wire galvanic erosion and allows the corresponding grinding wheels to be easily profiled and sharpened with maximum precision directly in the machine. It offers numerous benefits, including reduced wheel wear by approximately 70% and increased grinding power by at least 30%.
STUDER’s innovative SmartJet® technology provides customers with the industry’s only optimized refrigerant delivery, reducing the amount of water required by up to 40% and maximizing energy use compared to traditional solutions. 50% reduction. The system uses high-tech components, cutting-edge sensor technology, and 3D printed nozzles to work together.
New features in CORE and STUDER software
When it comes to high technology, digital development for intuitive operation, efficient production, cutting-edge sensor technology, smart data processing and visualization, as well as networking and automation capabilities are of particular importance to STUDER. In this field, there are important innovations in his CORE, his architecture of innovative hardware and software for the machines of the UNITED GRIND-ING group. All STUDER’s standardized automation solutions can now be operated via the intuitive icon-based his CORE panel. Moreover, the implementation of CORE in the portfolio has been further expanded to include all STUDER planned universal, external and internal cylindrical grinding machines with his CORE. In addition to your favorites, this now also applies to the series production cylindrical grinding machine S11 for small workpieces with StuderWIN.
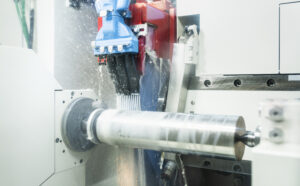
There are also innovative developments in the STUDER software. For example, his InOneThread, a new solution that will greatly simplify the task of grinding threads, will be released soon. For single-part production, InOneThread masters pre- and finish-grinding, measuring stops, temporary modification options and various intermediate dressing variations. In series production, customers benefit from time-optimized positioning of pre-machined screws and travel-optimized screw grinding. There are also new features in StuderWIN, the in-house software for quick and easy control of the grinding process. Latest enhancements include new radius grinding cycles, new cylindrical grinding pictograms for multiple shoulder grooving, and add-on customer tools.
We have the most advanced laser extensions for InOneControl. This is STUDER software for measuring workpieces in machines and is important for finishing and quality control of precision parts. Equipped with a new function (STUDER LaserControl™) for non-contact and highly accurate laser measurements. Thanks to a new measurement strategy, accuracy has been further improved. Additionally, it is now possible to program an air nozzle as a separate tool for blowing (cleaning) along the contours of the workpiece.