In today’s rapidly evolving world, manufacturing is at a crossroads. On the other hand, they must meet increasing demands for precision, speed, and customization. On the other hand, we must prepare for a future shaped by emerging technologies, the importance of sustainability, and increasing complexity. In this context, photochemical etching (PCE) is not just a manufacturing process, but is proving to be an important tool for enabling innovation and looking to the future.
PCE, a subtractive manufacturing technology that relies on photolithography and chemical etching to produce high-precision metal components, has long been recognized for its ability to create complex geometries without mechanical stress or tool wear. . But as the industry pushes the boundaries of what’s possible, PCE is evolving to meet new challenges, ensuring manufacturers stay ahead of the curve.
Advances moving PCE forward
One of the most exciting developments in PCE is its ability to process an increasingly diverse range of materials. Historically, metals such as stainless steel and copper were the workhorses of this process. However, innovations in chemical formulations and processing techniques have enabled PCE to use advanced materials such as amorphous metals and special alloys. This newfound versatility opens up opportunities across the industry. For example, aerospace manufacturers leverage PCE to create lightweight yet robust components, and medical device companies create corrosion-resistant and biocompatible parts for critical applications.
Another area where PCE is making progress is miniaturization. Industries such as telecommunications, electronics, and medical devices are demanding smaller and smaller components, and the precision capabilities of PCE are increasing to meet the challenge. Enhanced photomasks and more controlled etching solutions are making it possible to create components with finer features and tighter tolerances than ever before. In the medical field, for example, this precision has facilitated the production of implantable devices and surgical instruments with complex, burr-free geometries that enhance safety and functionality.
Sustainability is also a key driver of innovation at PCE. Unlike traditional manufacturing techniques, which often generate large amounts of waste and consume large amounts of energy, modern PCE processes are becoming increasingly environmentally friendly. Closed-loop chemical recycling systems and energy-efficient production lines reduce the environmental footprint of the process, making it an attractive option for manufacturers looking to meet stricter environmental regulations and sustainability goals. I am.
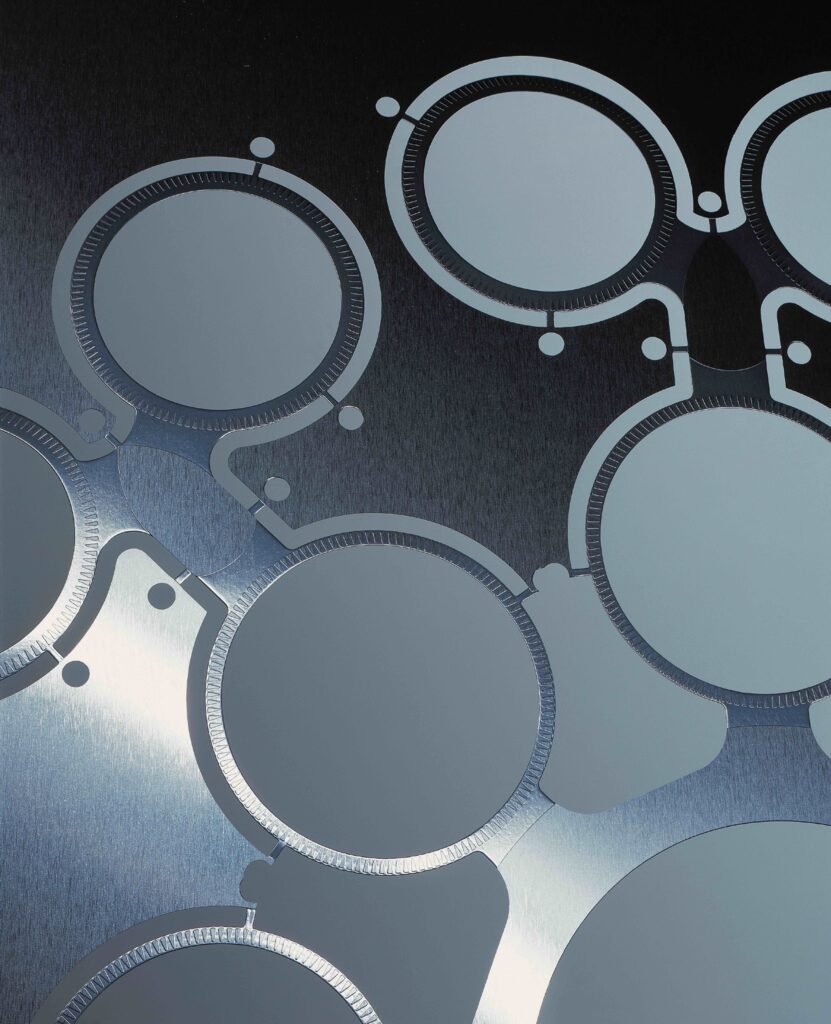
Applications across various industries
The versatility of PCE has led to its adoption across a wide range of industries, with each industry benefiting from the unique features of the process.
In the aerospace sector, where weight reduction is critical, PCE is used to manufacture components such as lightweight structural supports and complex fuel filters. PCE can create complex geometries without the need for expensive tooling, making it particularly valuable in this field where cost and performance are closely intertwined.
With stringent requirements for accuracy and reliability, the medical device industry is turning to PCE for applications ranging from stents to surgical instruments. The burr-free edges and fine details that can be achieved with PCE are critical to ensuring the safety and effectiveness of these components, especially in life-threatening applications.
In the electronics and communications sector, the rise of 5G and IoT technologies is driving demand for precision components such as RF shielding, circuit traces, and connectors. PCE’s ability to manufacture ultra-thin, distortion-free components is ideal for these rapidly evolving industries where even the smallest defects can impact performance.
The automotive sector is also benefiting from PCE, particularly in the development of electric vehicles. Battery housings, heat exchangers, and other lightweight components are produced using PCE, supporting the industry’s transition to greener transportation solutions.
PCE also plays a vital role in the energy sector. Perforated components for fuel cells and filtration systems, as well as complex parts for renewable energy technologies, are manufactured with the precision and efficiency that only PCE can provide.
Although PCE has many benefits, it is not without its challenges. This process requires careful control of variables such as temperature, chemical concentration, and exposure time, and relies heavily on expertise and precision.
However, the industry is already addressing these challenges through innovation. Automation, robotics, and advanced process monitoring systems are helping improve consistency and scalability. Artificial intelligence is also being applied to optimize component design and simulate chemical flows, reducing trial and error during production and increasing overall efficiency.
future
The future of PCE is inherently tied to the broader evolution of manufacturing. As Industry 4.0 technologies continue to take hold, PCE processes are becoming smarter, more efficient, and more integrated into complex production ecosystems. Automation enables faster and more reliable production, while data analytics and predictive maintenance ensure maximum uptime and productivity.
Emerging technologies such as quantum computing and flexible electronics are also creating new opportunities for PCE. For example, quantum systems require components with extremely precise shapes and minimal defects. This is a unique requirement of PCE. Similarly, in the field of renewable energy, PCE is being used to develop advanced solar panels, wind turbines, and hydrogen fuel cell components, contributing to the global transition to sustainable energy.
The integration of PCE with other manufacturing technologies is another interesting development. A hybrid manufacturing approach that combines PCE with additive manufacturing or laser processing enables the creation of components with unparalleled complexity and performance. This synergy is especially valuable in high-stakes industries such as aerospace and medical devices, where innovation often depends on the ability to push the boundaries of technology.
summary
As the industry faces increasing pressure to innovate and adapt, PCE has emerged as a critical tool to overcome the challenges of modern manufacturing. Its ability to deliver precision, flexibility, and sustainability is revolutionizing the way components are designed and manufactured, opening new possibilities in fields as diverse as aerospace, healthcare, electronics, and energy.
PCE’s journey is not yet over, but its trajectory is clear. As advances in materials, processes, and integration continue, PCE will play an even more central role in future manufacturing. For those willing to invest in its potential, the rewards are huge, including processes that are accurate yet adaptable, and technology uniquely equipped to meet the demands of a rapidly changing world. .
micrometal GmbH (combining HP Etch and Etchform) specializes in the industrial production of high-precision metal parts. The three companies photochemically etch millions of parts for a variety of industries with unique precision. Both companies etch a wide variety of metals and deliver clean, stress- and burr-free, customer-specific complex components. We combine the processes and expertise of micrometal, Etchform, and HP Etch to provide the right solution for every challenge. Together, the companies provide a one-stop shop for customers who want to benefit from world-class photochemical etching services.