Welding remains an important joining process in the metalworking industry and requires deep expertise and skill. Despite attractive salaries, the number of young people entering this profession continues to decline. This is because they are often considered unattractive, unhealthy and dirty. This is where collaborative robots come into play. Collaborative robots not only make welding more interesting and safer, but also make it more profitable, even with small batch sizes.
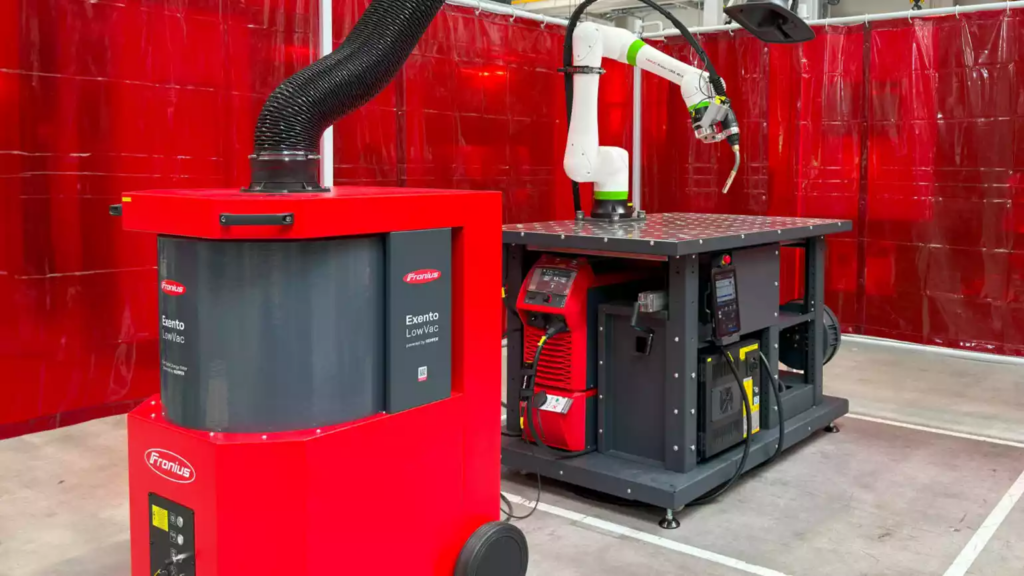
Cobots (collaborative robots) currently come in several types, including mobile individual workstations or fully enclosed one- or two-station solutions. A variety of technical equipment is available, including robotic tracks, turn/tilt positioners, automatic extraction systems, and safety doors. Today, high-tech welding machines, processes, and software solutions for offline programming often form part of standard equipment.
Times are changing and welding is becoming an increasingly high-tech profession. In addition to increasing productivity for commercial and industrial enterprises, welding automation will eliminate the growing shortage of skilled workers and make the welding profession cleaner, safer, and more attractive. Today, the career ladder for welders is high and ranges from welding specialist to international welding engineer (IWE).
Main advantages of cobot welding systems
Even the best welding experts cannot weld at a consistent quality level 24 hours a day. Cobots, on the other hand, easily learn this task and guarantee 100% reproducible and identical welds. Equipped with Fronius’ latest welding machines, such as the TPS 400i CMT and the multi-process version iWave 400i AC/DC CMT, you can weld a wide range of metals including steel, stainless steel, aluminum, copper and titanium. Innovative welding packages such as Low Spatter Control (LSC), Pulsed Multi Control (PMC), or the world-famous Cold Metal Transfer (CMT) are also available.
The LSC feature produces an improved low sputter dip transfer arc resulting in increased deposition rates. PMC offers an optimized pulsed arc and penetration and arc length stabilization to ensure the best welding quality and high welding speeds. CMT combines a new type of droplet separation with wire reversal action, which results in lower heat input than traditional dip transfer arcs. This makes the process particularly suitable for welding thin sheets.
“One of the main advantages of collaborative robot welding systems, especially the Fronius system, is how easy and intuitive it is to program the welding process. This makes it easy to start automatic welding.” emphasizes Christian Neuhofer IWS, Product Manager at Fronius International.
3 steps to welding program
Programming industrial robots requires both welding experience and solid programming skills. Collaborative robots are a completely different story. With the Fronius system, you simply grab the welding torch, guide it to the starting point, select the appropriate welding torch position, and press the save button on the control handle. Then set the contour points along the welding sequence to the end point. These points are saved at the push of a button and form the weld path. Once created, use the teach pendant’s graphical user interface to intuitively program your welding process with drag and drop.
“Compared to programming industrial robots, cobot education requires little training for most applications. Welding professionals, especially those who are accustomed to working with touch screens and have some computer skills, can weld their first component in just a few hours.” explains Neuhofer.
Valid welding parameters from smartphone
Thanks to the practical WeldConnect app, welding professionals always have their personal parameter manager at hand. The innovative online welding assistant provides professional support in choosing suitable welding parameters. These can be saved as jobs and transferred via NFC signals to the cobot system’s welder, allowing the welder to start welding immediately.
You can store numerous jobs in the WeldConnect app and access them at any time. Providing reliable welding parameters for a wide range of tasks, this app is especially appreciated by young welding professionals who are accustomed to using smartphones. Collaborative robots work with the WeldConnect app to help alleviate the skilled labor shortage and make welding an attractive career option again.
Mobile and flexible use: CWC-mobile by Fronius
Mobile cobot systems offer an intelligent combination of mobility, advanced welding technology, and great value. This makes it easier to introduce automatic welding technology, especially in small factories. Thanks to the retractable transport rollers, the system is also suitable for welding large parts.
“When you need to weld large items such as excavator buckets, you can easily push the CWC Mobile into ready-to-weld components.” said Neuhofer, emphasizing the system’s versatility.
In addition to flexibility when welding, the CE-certified collaborative robot system offers uncompromising safety. Articulated arm power and torque limiters, mobile welding fume extraction, mobile glare shield, and compliant personal protective equipment (PPE). Consists of perforated gloves, welding helmet and protective clothing to protect against illness and injury. This means that CWC Mobile fully meets the requirements of the European Machinery Directive. Prerequisites for CE certification.
Single and dual systems tailored to component dimensions and requirements
With the CWC-S and CWC-D, Fronius offers two fully enclosed collaborative robotic welding cells for one- and two-station operations. Like the CWC-mobile, both systems feature the latest welding technology.
The CWC-D two-station solution is ideal for welding components up to 3 meters long. Removing the central bulkhead, which is screwed to the welding table, creates an extended working surface of 3,000 x 1,000 x 600 mm for working in one station.
“Operating in two stations, the system is ideal for small-volume production of components with side lengths up to 1.5 meters, as welding can be carried out in parallel with set-up. You can increase productivity by performing welding on one side while adding equipment on the other side. Both stations can weld components weighing up to 2 tons” explains Neuhofer.
Smaller and more compact, the CWC-S has been specially developed for components up to 1.5 meters wide. Rotary and rotary/tilt positioners are available in both the CWC-S single system and the CWC-D dual system for circumferential welding of cylindrical parts. The turn positioner can optionally use a tailstock on the vertical axis. A coordinated motion software option available on all positioners allows you to move the welding torch and positioner in sync. The Robacta Reamer V Torch Cleaning Station is available as an accessory.
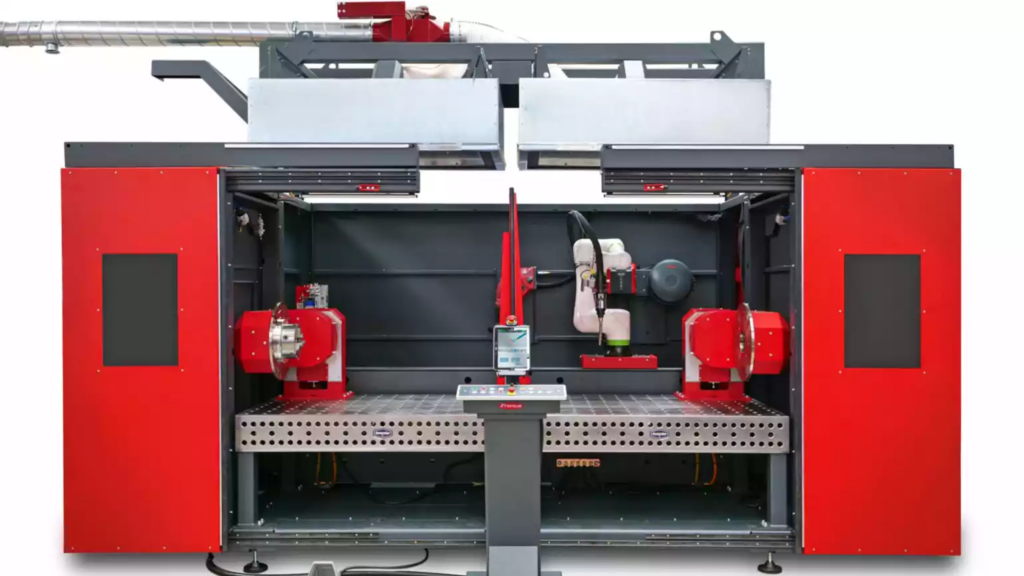
Integrate collaborative robots and welding robots
The fully enclosed Fronius cobot welding systems CWC-S and CWC-D enable seamless switching from cobot mode to robot mode. In this mode, power/torque monitoring and 250 mm/s speed limiter are disabled and speeds up to 2 m/s can be reached. In addition to faster articulated arms, programming with the iPendant robot controller allows you to perform more complex motion sequences and control your device in robot mode. This maximizes the system’s potential and significantly increases productivity.
Cobots are an ideal way to get started in the world of automation. This allows robot movements to be understood and kinematics to be learned by manual teaching without increasing the risk of injury. Welding professionals benefit from a deeper understanding of kinematic processes. This is especially advantageous if you later start working on robotic welding.
Increase productivity with offline programming
Fronius Pathfinder offline programming software allows you to program welding processes independently of the cobot welding system without interrupting ongoing production. Unlike manual teaching, software allows you to copy and mirror welds, create scanning processes, and simulate complex movement sequences. This minimizes downtime and increases productivity by up to 80%, especially for complex component geometries. As soon as the program is created, it is transferred to the welding cell and adjusted manually if necessary. Another advantage of Fronius is that the software and welding system come from a single source and work perfectly together.
High level of safety with Fronius collaborative robots
Fronius conducted a series of intensive safety tests in collaboration with external safety inspectors, with excellent results. These tests included attempts to puncture the gloves with wire, which were unsuccessful. The impact forces on the edges of the gas nozzle and torch holder were also measured and were safely within the prescribed limits. Particularly noteworthy is that the water-cooled welding torch turns to lukewarm water within seconds, effectively minimizing the risk of burns. All these results confirm that Fronius products meet the highest safety standards and ensure maximum safety.
The path to automation with Fronius
Fronius is close to our customers from the beginning, providing customized automation solutions from simple systems to complex applications.
“As a general contractor, we help our customers choose the optimal solution, including mechanization systems such as cobots, welding robots, welding trolleys, circumferential and longitudinal seam welding systems, seam welders, and track systems. Our advice doesn’t end after your purchase. We also have a global service network that supports our customers during commissioning and provides fast and reliable support in case of problems. This allows our customers to benefit from a high level of efficiency and safety in their welding processes.” concludes Neuhofer.
We are Fronius.
With more than 8,000 employees worldwide, the company currently has an 85 percent export share and 1,604 active patents. That’s us, that’s Fronius. Founded in 1945 as a local one-man operation, we are now a global company. This fact is clearly evidenced by our network of 38 international subsidiaries and distribution partners in more than 60 countries. However, at our core we are still an Austrian family-run company active in solar power, welding and battery charging technologies. We are constantly developing products and solutions for a future worth living, offering our customers an all-in-one package in the process, from advance planning and consulting to ongoing monitoring and repair services tailored to your specific needs. I did. We are innovative. We are curious. We are Fronius.
We are perfect welders.
The best vape quality, a deep understanding of our customers and a thirst for technological advancement are what drive us at Fronius Perfect Welding. We are an innovation leader in arc welding and a global market leader in robot-assisted welding. Automated complete systems and digital welding solutions customized for Industry 5.0 are the result of our expertise. Intuitive welding systems for manual welding applications, high-quality welding accessories and effective protection products for user safety complete our portfolio. As a global company, we provide local services through local teams serving customers around the world. Our technology breaks new ground and creates connections between metals, industry and people.