When machining high-temperature materials such as titanium and other superalloys, two factors are particularly important in controlling temperatures and maximizing downtime over service life: top-quality tooling and targeted coolant supply. play a role. The additively manufactured MaxiMill – 211-DC indexable insert milling system shows how proper nozzle positioning can make a real difference.
As anyone involved in machining titanium parts or superalloys can attest, the use of improvised strategies aimed at reducing costs and time is inevitable. Despite high speed machining, these incredibly tough materials simply make it difficult to ensure process reliability. “If these processes are to be carried out in even the slightest economically viable way, professionals often have to be willing to deviate from proven ‘roadmaps’ and try new strategies. No. For such stubborn cases, we developed the 3D printed indexable insert milling system MaxiMill – 211-DC,” says Robert Frei, Product Manager at CERATIZIT.
3D printing and precision cooling
Especially when processing titanium and other high-temperature materials, an optimized coolant is essential to achieve the highest quality results. This is where CERATIZIT’s patented shoulder mill shines. This is thanks to the precise placement of the coolant on the side of the milling indexable insert.
“Additive manufacturing processes are no longer just a nice-to-have; they are essential to achieving results not possible with traditional strategies. A prime example of this is our indexable Additive Manufacturing MaxiMill – 211-DC, which is an insert milling system,” says Frei. CERATIZIT recognized early on that 3D printing solutions had the potential to go beyond the limitations of traditional manufacturing processes and provide a viable alternative. Developed in-house and tailored to meet individual needs, these specially designed tools are manufactured additively.
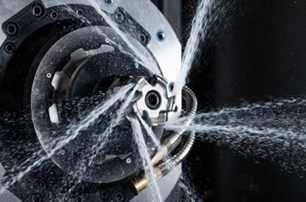
Out-of-this-world cooling precision
An example of the power of 3D printing solutions and additive manufacturing is the base body of the MaxiMill – 211-DC milling cutter. CERATIZIT’s engineering team sought to optimize the lateral cooling process, which is essential for machining titanium. “Our aim was to pour the maximum amount of coolant directly into the sides, which sounds very simple. However, achieving this required a very complex construction process, which It was only possible through additive manufacturing. In this way, the ideal In doing so, we were able to create the perfect combination of geometrical and functional properties, including a precise nozzle position and a precisely tailored insert shape for cooling. complete wetting can be guaranteed.
Despite the complexity of the large number of coolant holes inside the tool body, the MaxiMill –211-DC does not require standard coolant in the chip breaker and is compatible with standard adapters with coolant supply. Additionally, you get the same performance and benefits of using direct cooling for turning tools.
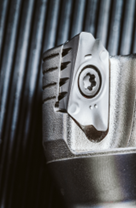
Maximized service life
To see where the MaxiMill with Direct Cooling – 211-DC really proves its worth, look at its service life compared to tools with standard cooling. 60% longer service life. “This additional service life enables fluid machining of titanium and superalloys while providing the benefits of a safe manufacturing process and minimizing tooling,” said Robert Freis of MaxiMill. – describes the use of 211-DC.
CERATIZIT – With a passion for hard materials and a pioneering spirit
For over 100 years, CERATIZIT has been a pioneer in the field of sophisticated hard material solutions for machining and wear protection. This private company, with its registered office in Mamer, Luxembourg, develops and manufactures highly specialized cutting tools, indexable inserts, hard material rods and wear parts. The CERATIZIT Group is a world market leader in various application areas and has successfully developed new carbide, cermet and ceramic grades, including for wood and stone processing.
CERATIZIT is a global company in the carbide industry with over 8,000 employees in over 30 production facilities around the world and a sales network of over 50 branches. The company’s international network includes the subsidiary Stadler Metalle and the joint venture CB-CERATIZIT.
CERATIZIT is a technology leader that continually invests in research and development and holds over 1,200 patents. CERATIZIT’s innovative hard material solutions are used in various sectors such as the automotive and aerospace industry, the oil and gas industry, mechanical engineering and tool manufacturing. medical field.